活用シーン
物流センターでの仕分け作業
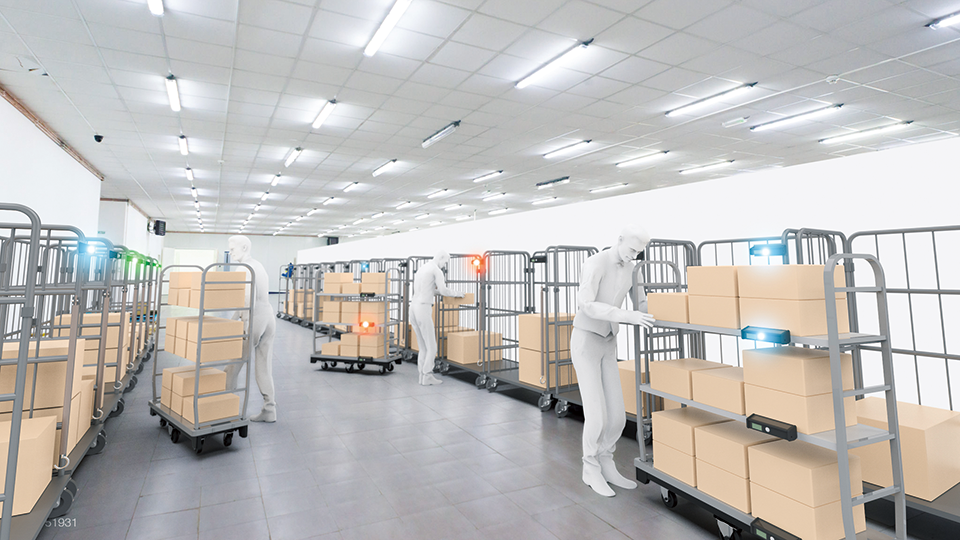
出荷先別に設置されたカゴ車に、入荷した商品を仕分ける作業に利用。
入荷した商品の6輪台車と、仕分け対象のカゴ台車に取り付けた表示器が同時に点滅し、個数を表示。それに従って仕分けを実施。
表示器を移動体に取り付けられるので、設備が固定化せず、現場スペースを有効活用できる。
食品工場での仕分け作業
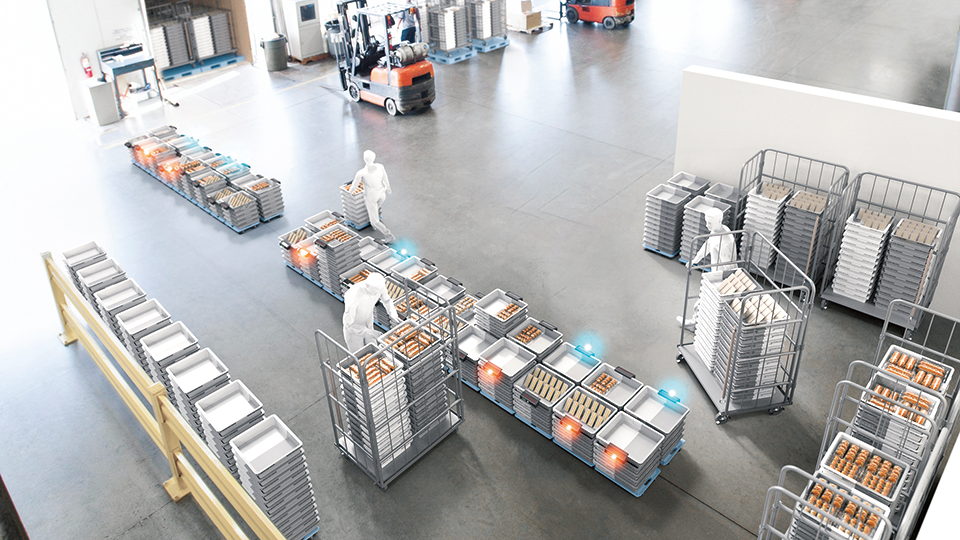
出荷先別に設置された容器に取り付け、食品を仕分ける作業に利用。
食品の専用コードを読み取ると、容器の表示器ランプが点滅し、液晶に個数を表示。ランプと液晶表示に従って仕分けを実施。
容器がいっぱいになって、新しい空の容器を置くときは、表示器を付け替えるだけで作業を継続できます。
作業量に合わせて、仕分けラインを自由に設定。
部品のマルチピッキング
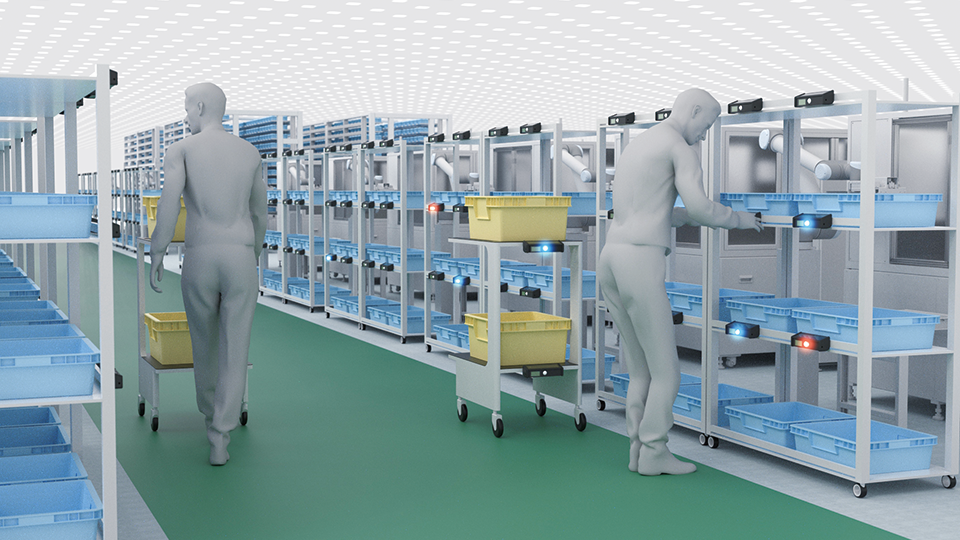
工場内にて部品のマルチピッキング作業に利用。
棚の表示器と手押し台車に乗せたコンテナの表示器が同時に点滅し、個数を表示。棚からコンテナにピッキングを実施。
作業が完了すれば、コンテナを次工程へ搬送。
ピッキングした部品を入れるコンテナに表示器を取り付けることで、マルチピッキングが可能。
生産工程の変更による棚の配置変えが容易。
搬送ロボット(AGV/AMR)と連携したマルチピッキング
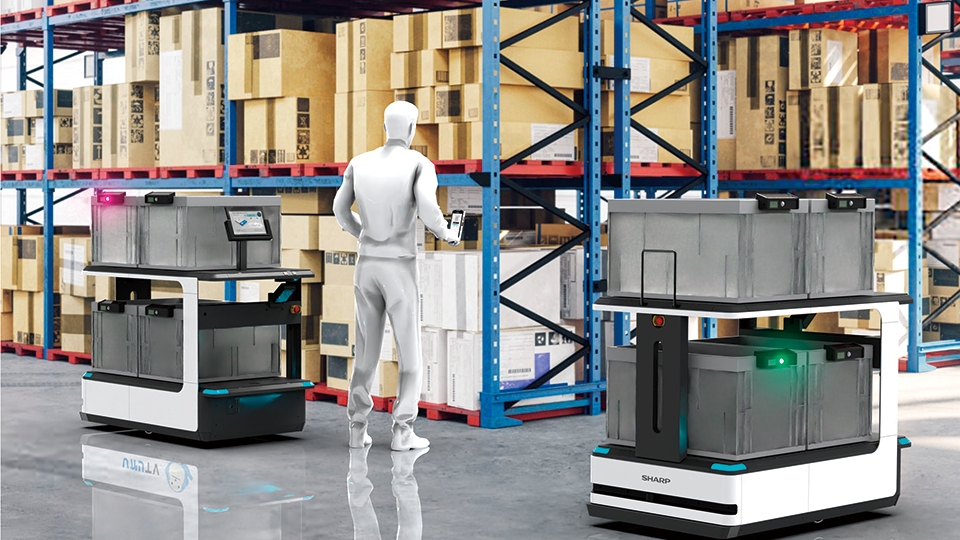
搬送ロボットと連携したマルチピッキング作業に利用。
搬送ロボットが目的の棚まで作業者を先導。
棚の表示器と搬送ロボットに乗せたコンテナの表示器が同時に点滅し、個数を表示。
棚からコンテナへピッキングを実施。
自動搬送ロボットと連携したマルチピッキングが可能。
RFIDリーダーを使用したポカヨケピッキング
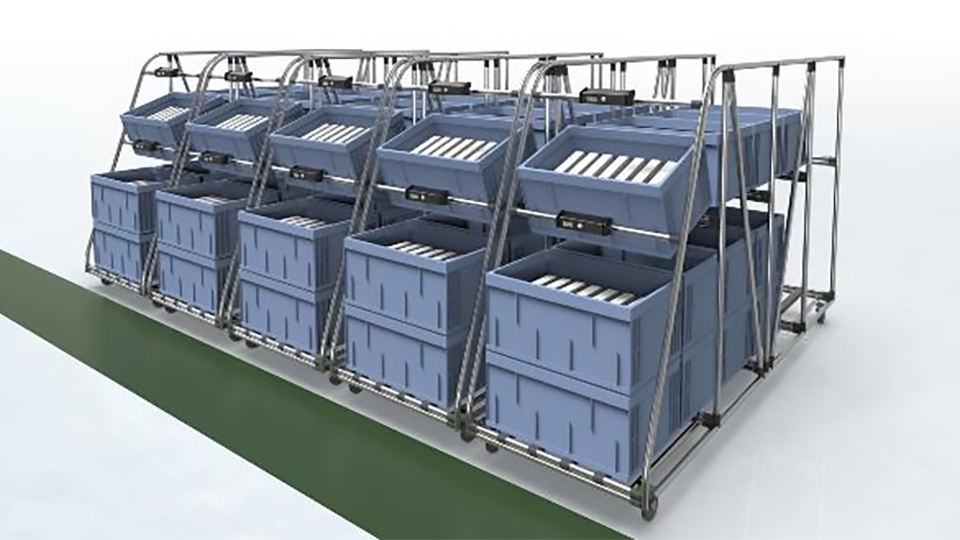
自動車工場の生産ラインでのピッキング作業に使用。
手首にRFIDリーダーを装着し、表示器にぶら下げたHFタグと照合しながら組み立てる順でピッキング。
RFIDリーダーを使用することで、ポカヨケが可能。
部品の組み立て順がわかる。